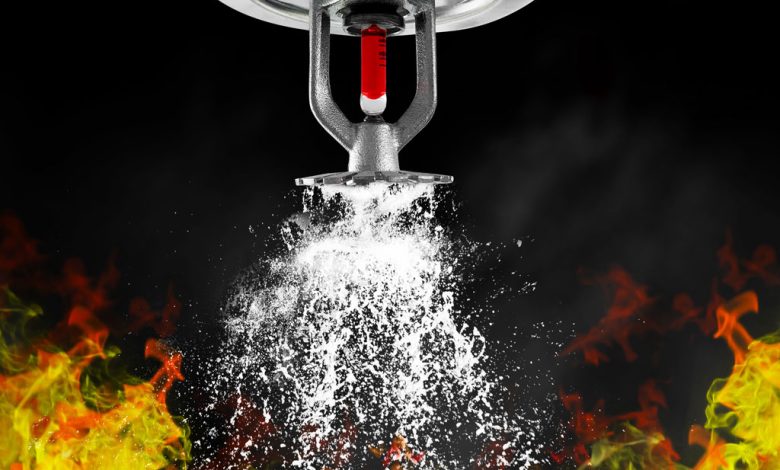
A properly functioning fire hydrant system is critical in any property’s fire safety strategy. Whether it’s a commercial complex, industrial site, or residential building, hydrants provide the first line of defense when fire breaks out. However, like all mechanical systems, hydrant networks can experience issues that compromise their performance. At Sri Triveni Crafts, we emphasize not just the installation of fire safety systems but also regular maintenance to ensure long-term reliability.
In this blog, we’ll explore common problems faced by fire hydrant systems and provide practical solutions to keep them running smoothly.
Why Regular Fire Hydrant System Maintenance Matters
When a fire emergency strikes, every second counts. A malfunctioning fire hydrant can delay response efforts, risking lives and property. Many issues arise due to lack of routine checks, aging components, or environmental exposure. By understanding potential failure points, property managers can ensure timely maintenance and avoid serious setbacks.
Common Fire Hydrant System Issues
1. Corrosion and Rust Formation
Problem:
Hydrants and associated piping, especially those exposed to moisture and oxygen, are susceptible to corrosion. This weakens the structural integrity and can lead to leaks or pressure loss.
Solution:
Use corrosion-resistant materials such as ductile iron or apply anti-corrosive coatings. Regular inspections should include visual checks and pressure tests to identify early signs of degradation.
2. Low Water Pressure or No Flow
Problem:
Insufficient water pressure renders the hydrant ineffective during an emergency. This could be due to sediment buildup, closed valves, or pump failure.
Solution:
Conduct periodic flow and pressure testing. Ensure that control valves are fully operational and that pumps and water storage systems are maintained and free of blockages.
3. Mechanical Damage and Wear
Problem:
Fire hydrants installed in high-traffic areas are vulnerable to accidental impacts from vehicles or machinery, leading to broken valves or bent nozzles.
Solution:
Install protective barriers or bollards around above-ground hydrants. Schedule mechanical checks to tighten fittings, lubricate moving parts, and replace damaged components as needed.
4. Valve Malfunction or Leakage
Problem:
Valves may stick, leak, or fail to open fully, especially when not operated for extended periods.
Solution:
Exercise valves regularly to ensure smooth operation. Lubricate internal components and replace worn gaskets or seals during scheduled maintenance.
5. Freezing in Cold Weather
Problem:
In colder regions, stagnant water inside hydrants can freeze, blocking water flow when it’s needed the most.
Solution:
Use dry-barrel hydrants in frost-prone areas. Ensure that the system is properly drained after each use and consider insulating exposed components.
6. Obstructed or Hidden Hydrants
Problem:
Hydrants may be blocked by vegetation, parked vehicles, or debris, making them hard to locate or access in an emergency.
Solution:
Maintain a clear radius around hydrants. Use signage or reflective markers to ensure visibility, especially in low-light conditions.
Best Practices to Prevent System Failures
1. Routine Inspection and Testing
Implement a monthly and annual inspection schedule to assess mechanical integrity, water pressure, and accessibility.
2. Recordkeeping and Compliance
Maintain detailed logs of all tests, repairs, and part replacements. Ensure compliance with local fire department and National Building Code (NBC) standards.
3. Training for On-Site Staff
Educate building or facility staff on how to operate hydrants during emergencies and conduct mock drills periodically.
How Sri Triveni Crafts Can Help
At Sri Triveni Crafts, we provide end-to-end solutions for your fire safety needs, including the design, installation, inspection, and maintenance of fire hydrant systems. Our expert team ensures that your system remains functional and compliant with all safety norms, so you’re never caught unprepared.
Conclusion
Even the best-designed fire hydrant system can fail without regular upkeep. Being proactive about inspections, part replacements, and pressure testing can prevent most common issues and ensure rapid response in emergencies. Partner with a trusted provider like Sri Triveni Crafts to maintain a reliable and compliant system that protects both people and property when it matters most.
Frequently Asked Questions (FAQs)
1. How often should a fire hydrant system be tested?
It should be inspected monthly and undergo a full performance test at least once a year.
2. What causes low water pressure in fire hydrants?
Common causes include sediment buildup, pump malfunction, or closed gate valves in the supply network.
3. Can a fire hydrant freeze in winter?
Yes, hydrants can freeze in cold climates. Dry-barrel hydrants and proper draining practices can prevent this.
4. What is the life expectancy of a fire hydrant system?
With proper maintenance, components can last 20–50 years, though individual parts like seals and valves may need more frequent replacement.
5. What should I do if I suspect a hydrant on my property is damaged?
Contact your fire safety provider immediately for an inspection. Avoid operating it until it’s assessed and repaired.